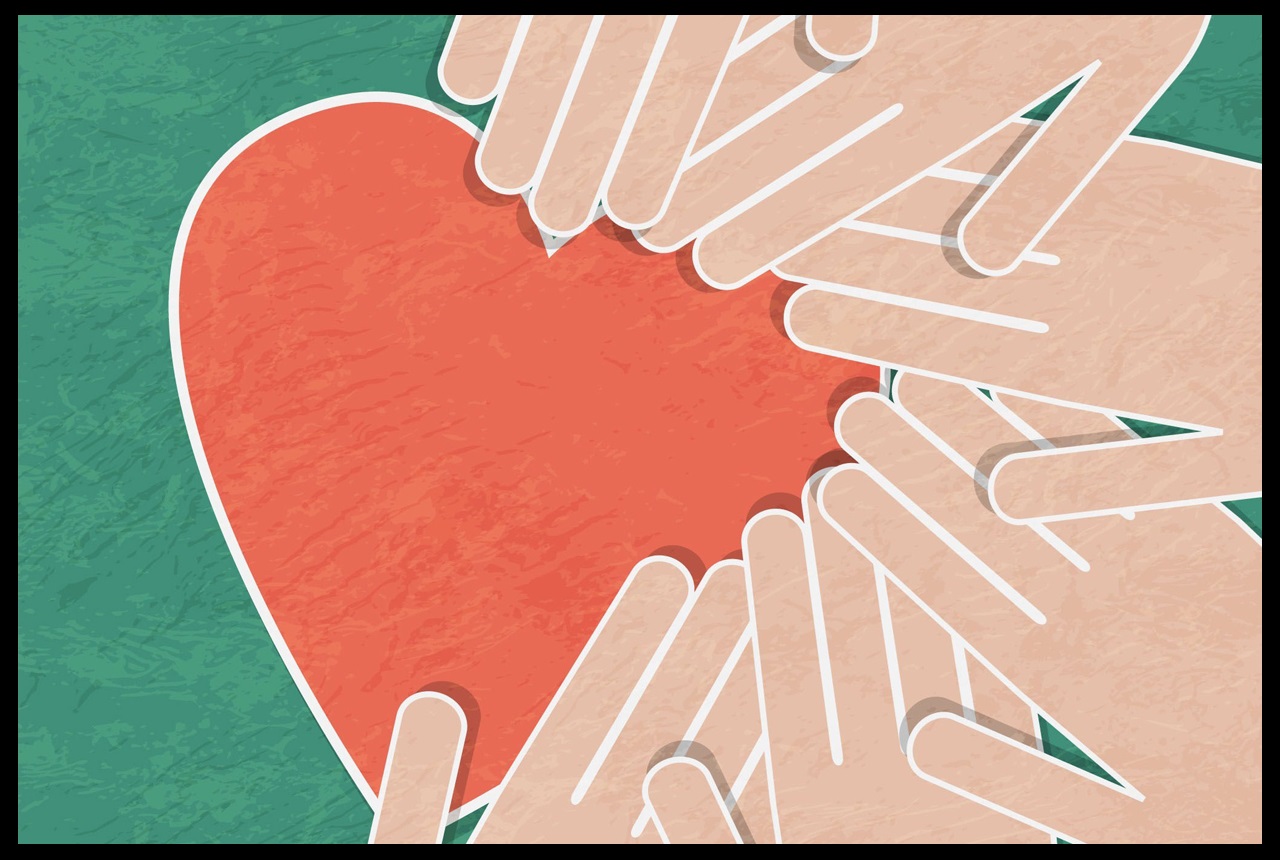
“The Toyota Way,” “Lean”—we’ve all heard the terms and been exposed to the buzz. We know that the Toyota Production System model is admired and emulated the world over by management experts and gurus. But it’s not news—it’s not the latest-and-greatest—so, why should we care now? Here’s why: The Toyota Way, or Lean, works. Its effect in helping healthcare organizations and entire health systems improve patient care, reduce errors, increase patient and staff satisfaction and more is well-documented—indeed, proven. Why, then, wouldn’t we want to know all about it?
Derived from the waste-reduction, just-in-time management philosophy implemented in Japanese car manufacturing in the 1930s and 1940s, Lean has since emerged as a potent tool to help healthcare leaders provide smoothly operating, patient-centered care free from errors. In healthcare, waste is conceived as anything that doesn’t add value. In patient-centered healthcare, value is regarded as only those items and services a patient would willingly pay for out of pocket. The waste to be eliminated, then, comprises unnecessary wait times, lengthy travel between service centers, redundant forms to complete and staff to inform, all manner of inefficiencies and, most particularly, errors and injuries in patient care.
At ACHE, through the Leading a Culture of Safety blueprint jointly developed by ACHE and the IHI Lucian Leape Institute, we’re extremely focused on helping our members transform their institutions and agencies into high-reliability organizations founded on a culture of safety. Implementation of Lean is one surefire way to move your hospital or health system closer to the goal of zero patient harm.
ACHE members have access to the second edition of The Toyota Way to Healthcare Excellence: Increase Efficiency and Improve Quality with Lean by John Black (with David Miller and Joni Sensel). This new edition provides detailed information regarding the implementation of Lean in the massive Saskatchewan provincial healthcare system as well as reports and historical perspectives from three leaders who have implemented Lean in U.S. health organizations for a decade or more.
What do these leaders want us to know? Dr. Gary Kaplan, CEO of Virginia Mason Medical Center in Seattle and chair of IHI Lucian Leape Institute, is one of the earliest Lean healthcare pioneers. In his foreword to the second edition, Kaplan is effusive. He professes that at Virginia Mason, Lean has led to: “…significant improvements—contributing to at least a 50 percent reduction in time, space, or the need for other resources. In areas of major focus, we’ve seen defects go to nearly zero. We’ve experienced improvements in the hospital length of stay, patient wait times to see a doctor, face-to-face time for patients with their physicians, time to get lab results, and even time to get the bill sent out.…Lean works!”
Kaplan promises that healthcare executives can “create a better, safer, more efficient, and higher quality healthcare system if we are willing to embrace these new methods and are truly willing to lead.”